As the world shifts towards a more sustainable and environmentally conscious future, the recycling of lithium-ion batteries has become a critical focus. One of the most effective and widely used methods for recovering valuable materials from these batteries is the hydrometallurgical recycling process. This article will provide a comprehensive overview of the hydrometallurgical recycling process, its benefits, and the key steps involved.
Understanding Hydrometallurgical Recycling
Hydrometallurgy, also known as wet metallurgy, is a branch of extractive metallurgy that uses aqueous solutions to recover metals from their ores or other solid materials. In the context of battery recycling, hydrometallurgical processes are used to extract and purify valuable metals such as lithium, cobalt, nickel, and manganese from spent lithium-ion batteries. This method is highly efficient and environmentally friendly compared to other recycling techniques like pyrometallurgy, which involves high-temperature smelting and can be more energy-intensive and polluting.
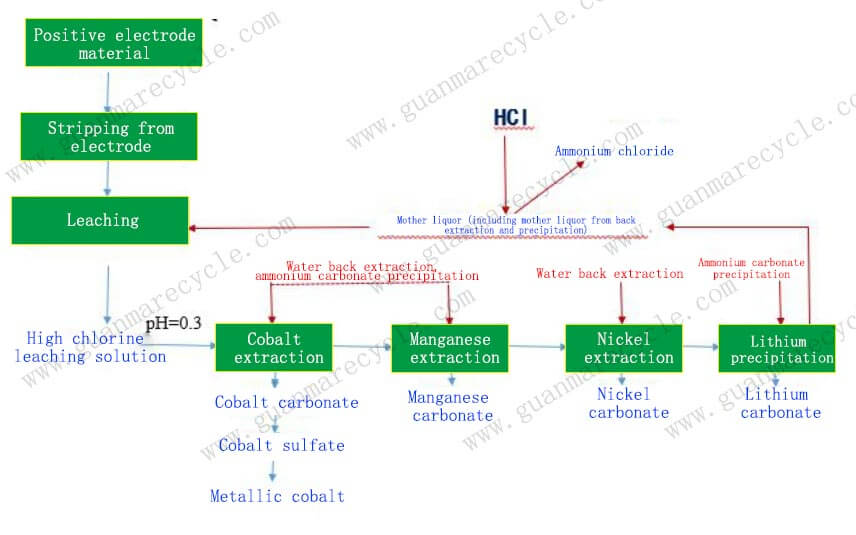
Key Benefits of Hydrometallurgical Recycling
1. High Recovery Rates
Hydrometallurgical processes can achieve high recovery rates of valuable metals, often exceeding 90%.
2. Environmental Friendliness
The use of aqueous solutions reduces the environmental impact compared to high-temperature processes, which can release harmful emissions.
3. Flexibility
Hydrometallurgical processes can be adapted to handle different types of batteries and varying compositions of cathode and anode materials.
4. Cost-Effectiveness
While the initial setup costs can be significant, the operational costs are generally lower due to the efficiency of the process and the value of the recovered materials.
Steps in the Hydrometallurgical Recycling Process
1. Collection and Pre-Treatment
The first step in the hydrometallurgical recycling process is the collection and pre-treatment of spent lithium-ion batteries. This involves:
Sorting and Disassembly: Batteries are sorted based on their type and condition. They are then disassembled to separate the various components, including the cathode, anode, and electrolyte.
Mechanical Processing: The disassembled components are mechanically processed, typically by crushing and grinding, to reduce them to a fine powder. This step increases the surface area, making it easier for the subsequent chemical reactions to occur.
2. Leaching
Leaching is the core step in the hydrometallurgical process, where the valuable metals are dissolved into an aqueous solution. These agents form stable complexes with the metals, enhancing their solubility and selectivity.
The choice of leaching agent depends on the specific composition of the battery materials and the desired purity of the recovered metals.
3. Purification
After leaching, the solution contains a mixture of dissolved metals. The next step is to purify the solution and separate the individual metals. This can be achieved through several techniques:
Precipitation: By adjusting the pH or adding specific reagents, the metals can be selectively precipitated out of the solution.
Solvent Extraction: This technique uses organic solvents to selectively extract the metals from the aqueous solution. The metals are then back-extracted into a new aqueous phase, allowing for further purification.
Ion Exchange: Ion exchange resins can be used to selectively adsorb and desorb the metals, providing a high degree of purification.
4. Metal Recovery
Once the metals are purified, they can be recovered through various methods:
Electrodeposition: The purified metal ions can be reduced to their metallic form through electrochemical deposition. This process is commonly used for the recovery of copper, nickel, and cobalt.
Crystallization: For some metals, such as lithium, the purified solution can be concentrated and cooled to form crystals, which can then be dried and packaged.
Thermal Reduction: In some cases, the metal compounds may need to be thermally reduced to produce the pure metal. This step is often used for the recovery of lithium and manganese.
5. Post-Processing and Waste Management
The final step involves post-processing the recovered metals to meet the required specifications and managing any waste generated during the process. This includes:Refinement and Alloying: The recovered metals may need to be further refined and alloyed to meet the quality standards for reuse in new batteries or other applications.
The hydrometallurgical recycling process is a powerful and environmentally friendly method for recovering valuable metals from spent lithium-ion batteries. By following the detailed steps of collection, leaching, purification, metal recovery, and waste management, this process can achieve high recovery rates and contribute to a circular economy. As the demand for lithium-ion batteries continues to grow, the adoption of hydrometallurgical recycling will play a crucial role in ensuring the sustainability and resource efficiency of the battery industry.
If you are interested in learning more about the hydrometallurgical recycling process or exploring the equipment and solutions available for your recycling needs, please contact us or visit our website.